Do you know the pros and cons of welded vs bolted pallet rack? When you’re ready to increase your warehouse space’s storage, you must consider many factors in developing the right solution. One of the first decisions you’ll face is determining the right pallet rack storage system. Many companies in North America utilize welded racks. In comparison, companies throughout Europe and the rest of the world prefer bolted racks. Both fastening technologies are useful for constructing racks. Still, they offer distinct advantages and disadvantages regarding structural integrity, durability, customization, and cost of production, shipping, installation, and repair.
Consult the resource below for an in-depth comparison of welded vs bolted pallet racks, then contact American Material Handling to get started on your warehouse upgrade. Our team can examine your space to create a personalized solution that fits your business goals and budget.
Welded vs Bolted Pallet Rack: What’s the Difference?
Welded pallet rack frames are constructed by welding the cross-bracing or struts to the frame columns, often directly attaching them to the open lips of the “C” shaped column channel. Manufacturers construct bolted pallet rack frames by bolting the frame struts or brace panels to the sides of the “C” shaped channel using pre-drilled holes to accommodate the supporting hardware.
Structural Integrity
While neither system claims to be the best for structural integrity, the different construction methods for creating welded and bolted pallet racks play a crucial role in the structure’s ability to withstand applied forces. Bolted racks most closely resemble typical building designs for large warehouses, retail structures, and skyscrapers. These are nearly 90% steel posts and beams, bolted together to form the underlying structure.
Flexibility and Bracing
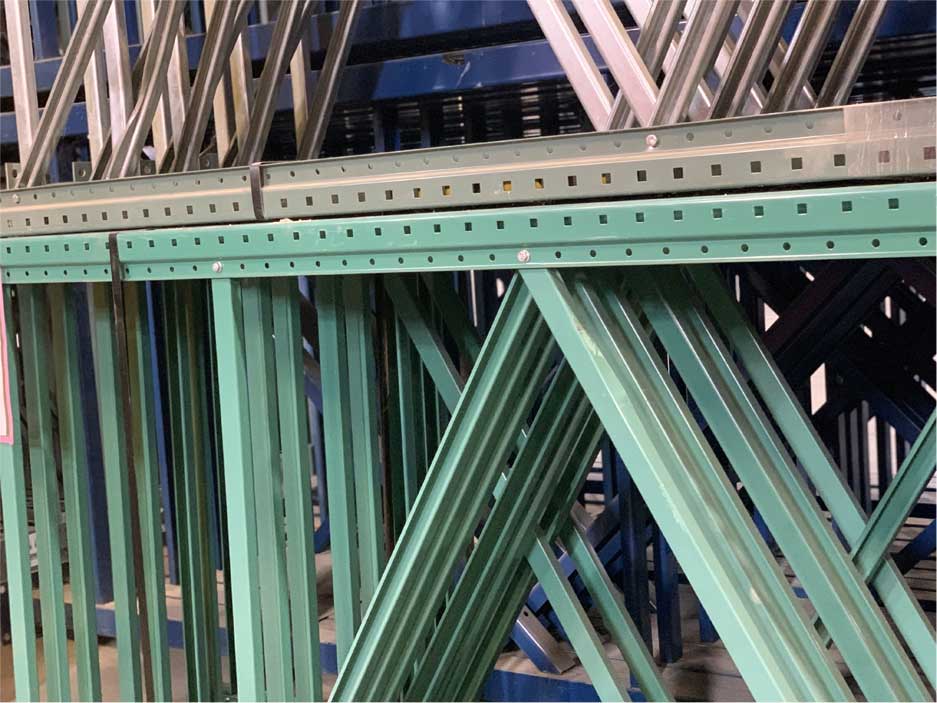
Bolted bracing members are not rigidly fixed to the column lips. Instead, they form a connection with a single bolt. Because of this, they can withstand applied forces while preventing movement from being transferred across the joint. The flexibility allows buildings to experience forklift impacts, seismic events, record wind gusts, and other applied forces without transferring the force or breaking. Because of this, the design makes pallet rack construction very sturdy.
In contrast, welded bracing members are rigid and fixed in place. This rigidity means they cannot flex in response to subtle earth movements and other bending forces. It also means they are more likely to break during seismic events.
The flexibility of bolted frames should make them the clear choice for areas with frequent seismic activity. However, this is up for debate. Some experts claim that the structural integrity of welded racks is stronger than bolted racks. This is when welded systems have offset or slope-back front legs or feature seismic full-depth base plates. This design lets workers place the beams at ground level. A professional can help you take your warehouse location and potential seismic activity into account to determine the right solution for your space.
Durability
A common misconception about bolted pallet racks is that bolts become loose over time and require tightening to avoid compromising the structural integrity of the rack. In fact, these locking bolts have serious durability. Their serrated lock nuts and limited bolt threads prevent overtightening. After the manufacturer tightens the lock nuts, they are effectively locked in place. They will not become loose, even if the entire rack assembly ships in one piece. If shipped in multiple pieces, the installer will tighten the lock nuts on-site.
If a rack does endure some type of damage, a bolted frame can continue providing support to the structure until someone can remedy the issue. In contrast, a welded frame can collapse. This makes damaged welded uprights far more dangerous than damaged bolted uprights. For example, if a lock nut came off the structure, which is extremely unlikely, or a column or strut suffered damage, the bolt would still support the system. On the other hand, a faulty welding job undermines the structural integrity of the welded pallet rack. Without prompt attention, it can take down the entire structure as well as seriously injure your staff.
Customization
Customizing a bolted pallet rack to your specific needs is a simple, easy process. It involves cutting the columns down to the appropriate size and adjusting the bracing during the assembly of the frame. However, to customize a welded pallet rack, the manufacturer must remove a diagonal and/or horizontal brace from the structure, cut down the columns, and re-weld the bracing. This process is much more complicated, time-consuming, and expensive than customizing bolted racks. In some cases, it is not even possible to make adjustments that meet the client’s specifications.
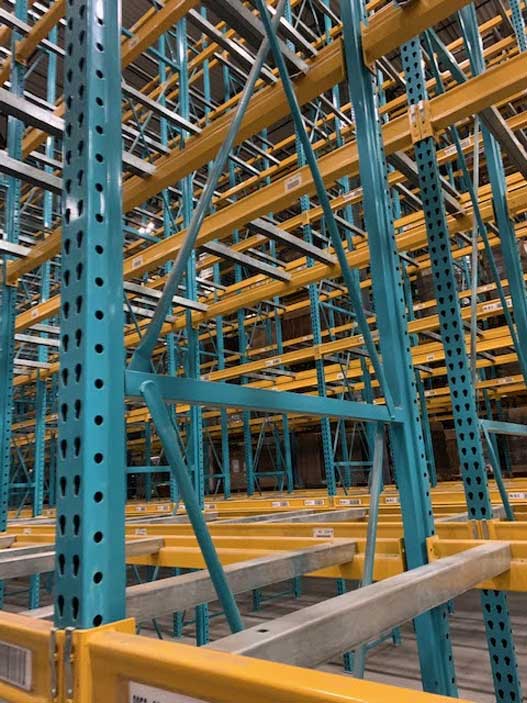
Cost
Bolted pallet racks cost less than welded pallet racks in terms of production, shipping, and installation. Although the components used in both systems are nearly identical, bolted racks involve a lower production cost because they do not require the added labor and material costs of welding. Adding a galvanized finish is required in pharmaceutical and food handling applications. This drives up the cost of a welded system. The higher cost is because the uprights cannot be galvanized until after the construction of the rack.
Price Comparison
The cost to ship a bolted rack is significantly less than shipping a welded rack. This is particularly true when the uprights come in pieces, where the team assembles them on site. A truck can carry double the equipment when transporting bolted uprights than when transporting welded uprights. Additionally, welded uprights can cost twice as much to ship because they are pre assembled and take up more space. A forty-foot truck of welded uprights can only hold 20,000-25,000 pounds. A truck of the same size carrying “knocked down” bolted uprights can hold up to 48,000 pounds, allowing you to transport more equipment in fewer trips. This saves time and money.
Along with being cheaper to manufacture and ship, bolted pallet racks are also less expensive to install. After the bolted rack arrives, it is much easier to handle and unload than a welded rack. It is also easier for the installation team to reconfigure it into the final structure. Bolted pallet racks may cost more initially to install than welded pallet racks. However, the installers do not have the same level of skill and experience as a certified welder in a manufacturing plant. They tend to work for lower wages, reducing the overall labor cost and quickly getting your new system in place.
Ease of Repair
When comparing welded vs. bolted pallet racks, another advantage of the bolted rack is the ability to easily unbolt bent or damaged bracing. This way, you can repair it with new bracing in the event of damage. Suppose an incident occurs and the rack does need repair. In that case, you can easily make a visual examination of the structure to determine the issue and decide on the correct course of action. If the bolted rack attaches with a bolted base plate, you can repair the strut or column in the field with only a ratchet and band saw.
This contrasts with welded joints, which may seem acceptable from the outside but can hide an adequate or unreliable connection that could threaten the entire structure. Unlike issues with bolted uprights that are typically apparent to the naked eye, diagnosing damages or defects in welded uprights requires performing further testing. Fixing the problem usually involves cutting off the damaged area with a torch and building expensive, custom replacement parts.
Contact Us Today
If you are a business professional in warehousing, storage, or fulfillment and want to expand or rearrange your current facility, contact American Material Handling today. Likewise, if you’re looking to open a new facility, we can help. For nearly four decades, our family-owned business has helped thousands of clients across various industries operate their businesses more efficiently. We help our clients deliver the best results to their own customers.
Our industry-leading team can work with you to design a customized solution for your exact warehouse specs. Together, we can develop a plan for your storage needs so you can maximize your space. Then, we will show you how it will look with our 3D Modeling Service. Once you approve the equipment and layout, we can move forward with installation. Talk to our experts today or call (888) 490-1181.